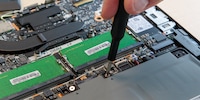
Product test
The collaboration between Lenovo and iFixit has not yet reached its goal
by Jan Johannsen
His dream is a modular ThinkPad, but the next step is to make the USB-C port interchangeable. An interview with Christoph Blindenbacher from Lenovo.
In spring 2024, Lenovo presented the first ThinkPads manufactured in cooperation with iFixit. This collaboration makes them easier to repair. Christoph Blindenbacher, Director Thinkpad Portfolio Management at Lenovo, is jointly responsible for this. In this interview, he talks about how the cooperation came about and reveals what Lenovo expects from "repairing instead of buying new".
Mr Blindenbacher, when did Lenovo start focussing on the repairability of notebooks ?
About five years ago, we wanted to know why our commercial notebooks were being replaced after just three to four years. We wanted the Thinkpads to be usable for longer. It turned out that employers thought that the laptops no longer had enough value for the employees.
Are we talking about hardware upgrades or the repair of defective components?
Upgradeability was among the top 3 priorities. This was followed by the ability to replace the keyboard and battery. The most important criterion as to why new devices were purchased was the value, or rather the signs of wear and tear on the keyboard. However, this only applies to the enterprise environment, i.e. business customers and ThinkPads. The situation is certainly different for our Ideapad or Yoga consumer notebooks.
Covid caused an additional push in the area of retrofittability. With the shift to working from home, some applications that require more computing power became more important. However, Microsoft Teams and similar programmes primarily require RAM and not necessarily more CPU power. That's why we have made the RAM bars in particular easier to replace.
Which component do you want to make interchangeable next?
The USB-C port. This is now the most frequently used port and it is correspondingly annoying when it wears out. It is currently still located on the mainboard. This makes repairs time-consuming and expensive. We want to place it and other frequently used connections on individual cards so that the entire mainboard does not have to be replaced. The basic philosophy behind the T14 model can already be seen in the Ethernet port. This can already be replaced quickly - but so far only by our service team and not by the customers themselves.
And how quickly did repairing instead of selling new equipment catch on with a computer manufacturer?
Of course, as a company we also want to sell notebooks. Something like the Thinkpad T14 is already a big change in philosophy that required a lot of discussion among Management. Of course, it helped me to argue that sustainability is currently a trend. As a company, we have the goal of becoming CO₂-neutral by 2030. This is also relevant for many business customers. Easy-to-repair laptops that can be used for longer help to achieve such goals. This brings us back to the keyboard and battery. These components are the main reasons why customers buy a new laptop, even though the rest of the computer is actually still perfectly usable.
I have heard from smartphone manufacturers that inferior replacement batteries were one of the reasons for permanently installing batteries. How does Lenovo intend to prevent similar problems with the much larger notebook batteries?Of course, we could say that customers should simply use our batteries. But within the framework of legal regulations, the first states are already demanding that customers must be able to install batteries from any manufacturer. This is where we are challenged. We have to ensure that batteries from third-party manufacturers do not pose a risk. One possibility is to work with algorithms. These can, for example, recognise the condition of a battery or count the charging cycles. However, this is a challenge that not only Lenovo is facing.[[image:76500466 "The battery of the Thinkpad T14 has a plug connection." "Jan Johannsen"]]Since you just mentioned regulations: Are such requirements, for example those of the EU with regard to reparability, annoying obligations or do they help to be able to enforce certain ideas within the company?That helps me in that sense. Such guidelines also apply to everyone. In my product area, however, it's a bit easier, as business customers have different requirements. My colleagues from the consumer sector, for example, would find it much more difficult to make a notebook three millimetres thicker so that the keyboard is replaceable. The hardware departments of companies, on the other hand, are very happy about this.The important thing is to stay up to date with such requirements and to know what to expect in the future. We are very happy to have iFixit as a competent partner at our side. The next big step is the EU requirement that batteries in all devices must be replaceable. From 1 January 2027, this will apply not only to notebooks, but also to smartphones, for example. That will change a lot.Did iFixit approach you or did Lenovo turn to the repair experts?We approached iFixit. They already had a great deal of expertise on the various laws, which vary greatly from country to country. France, for example, is even stricter than the EU as a whole. And in the USA, more and more states are introducing a "right to repair". We wanted to have experts who only deal with this topic. [[image:76500461 "The Thinkpad T14 was co-designed by iFixit." "Jan Johannsen"]]How satisfied is Lenovo with the cooperation so far?We have not only utilised iFixit's general advice, but have also involved them directly in the development of two notebooks in the T and L series from the very beginning. We are very satisfied with the result and have just discussed the framework conditions for a further long-term collaboration with them. I think this partnership was the best decision we could have made.iFixit has the spare parts in stock and designs repair instructions.Yes, they helped us there too. They also assess repairability according to transparent criteria. This creates good comparability for customers. They have set standards there and remain independent despite working with us.Theoretically, other manufacturers could also go and get an iFixit score for their notebooks.Yes, Microsoft has imitated us a bit. We also know that other manufacturers have come knocking. Which makes us very happy, because it shows that we have set a certain new standard. And we are getting extremely good feedback from customers.Can you summarise the simple means of making it easier to repair a notebook in general?First of all, it is very important not to use anything proprietary. If you look at the Thinkpad T14, we use normal Philips screws (Phillips head, editor's note). We also use as few screws as possible and instead use other fasteners that don't require glue. For our Thinkpad, however, we have additional requirements in terms of robustness. Screws are currently the best option there.[[image:76500464 "Screws are the best fastener for Lenovo." "Jan Johannsen"]]Unique markings ensure that people recognise which components they can replace. And then the repair guide must be kept very simple. Preferably a guide with lots of pictures or as a video to fulfil different needs. All repairability aside, safety must also be guaranteed. Customers should not be able to injure themselves or accidentally destroy anything. That's why the battery has a thin metal cover to give it more stability. Without this, there would be too great a risk of it bending when removed or being damaged by a falling screwdriver. The grey colour also provides a colour contrast and makes it easier to see black screws or other objects lying on it. What else can we expect in terms of repairability in the future?Repairability is a strategic portfolio requirement - and will remain one. Alongside price, sustainability is now the most important purchasing criterion in the business environment. I'm sure that the next step will be to make the connections interchangeable regardless of the mainboard. As a first step, however, end users may not yet be able to do this themselves. In addition, we can certainly make it even easier to show users what they can repair and how to access the necessary information.So that the user doesn't damage anything during the repair, we could, for example, better protect the circuit board from contact and introduce simpler plug connections. This could also reduce the fear of losing the warranty during repairs. Does this apply to all Lenovo notebooks?I can only speak for my division. I don't know the plans of my consumer colleagues in detail. We are still in the process of finding out how far customers are prepared to compromise. We sell the T or L series to people other than the Thinkpad X1. The design and the very flat construction play a much more important role here. The batteries will have to be replaceable in all devices from January 2027 due to the EU directive. But whether we make the keyboard of even more notebooks easily replaceable, for example, also depends on customer demand. I found the Framework laptop very exciting. It has a modular concept and has been on the market for a few years now. For example, it has four slots where you can easily change the connections as required.Yes, the framework is a very interesting concept, but you always have to ask yourself where you compromise on quality. But we have of course looked at the device in detail, as it has already set a small trend. [[marketingpage:21955]]This has led to a lot of questions for us. I love the modular ports, but we would have to build our devices deeper for that. That's a decision you don't make so quickly. The framework design also harbours risks in terms of the longevity of the devices.If you ask me, framework is my goal. How do we get a framework with the Thinkpad characteristics in terms of quality?Technologically, we are not yet where we want to be. And then there's the awareness of private customers. For many, sustainability is not yet a relevant criterion. However, I think that we will gradually promote this awareness by complying with the relevant regulatory requirements.
As a primary school pupil, I used to sit in a friend's living room with many of my classmates to play the Super NES. Now I get my hands on the latest technology and test it for you. In recent years at Curved, Computer Bild and Netzwelt, now at Digitec and Galaxus.