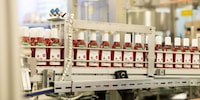
En coulisse
Comment crée-t-on un shampooing bruyant ?
par Natalie Hemengül
Gros coup de fatigue... Après sept heures passées à recevoir des informations sur les matelas, mon cerveau aurait bien besoin d’une petite sieste. Reportage dans l’usine de matelas Bico à Schänis.
Je passe huit heures par jour allongé sur ce grand carré blanc qui me sert de matelas, et qui fait plutôt bien son travail. Il faut dire qu’il n’était pas donné. Il y a deux ans, après avoir reçu des conseils dans un magasin spécialisé, ma femme et moi avons déboursé une somme à quatre chiffres (par personne) pour un nouveau matelas et sommier.
À l’époque, j’avais un peu eu l’impression d’avoir été victime d’une opération marketing. Alors lorsqu’au détour d’une conversation j’ai pu faire la connaissance de Jens Fischer, responsable marketing chez Bico, mon instinct de chasseur s’est réveillé. Après tout, c’est chez ce fabricant suisse que j’ai acheté mon matelas de luxe.
Pour un sommeil sain et profond.
Après quelques échanges amicaux par e-mail, le moment était enfin venu : j’allais être autorisé à assister à la fabrication des matelas. En compagnie du photographe Chris Walker je pris la route vers Schänis, petite bourgade de 3800 habitants située entre le lac supérieur de Zurich et le lac de Walenstadt. C’est ici que se trouve Bico, une marque du groupe suédois Hilding Anders.
Bico est née Birchler und Co. à Reichenburg, dans le canton de Schwytz. Le « Bi » de Birchler et le « Co » sont devenus Bico AG en 1961. En 1962, l’entreprise conquit les lits suisses avec « Isabelle », le tout premier matelas en mousse sans ressorts en acier. Un véritable carton encore fabriqué aujourd’hui en quatre variantes, différents degrés de dureté et tailles. « Isabelle » est devenue une gamme à part entière chez Bico, proposant même des duvets et des sommiers.
Tous les modèles naissent dans l’usine de matelas située au siège de l’entreprise à Schänis. Les alèses ont des noms qui claquent comme « Body Fine », « Body Luxe », « Clima Pro » et « Vita Feel ». De quoi moderniser un peu l’usine bleue et grise qui semble tout droit sortie des années 70. Lors de notre visite, nous sommes accompagnés par le responsable marketing et Rocco Cristofaro, responsable innovation chez Bico.
Le bâtiment, qui fait penser à un atelier de couture surdimensionné, pourrait facilement accueillir un terrain de football. À dire vrai, les tissus cousus ici font généralement au moins 90 cm sur 200. Cela correspond à la dimension de la moitié des matelas vendus par Bico.
Mais commençons par le commencement : l’intérieur du matelas. Pour ce faire, nous nous rendons d’abord à Wolfhausen, village de la commune de Bubikon. C’est ici que l’entreprise Foampartner AG a installé son siège.
En général, difficile de voir ce qui se cache sous le tissu d’un matelas. Les vendeurs et vendeuses des magasins de literie montrent parfois l’intérieur de leurs produits à la manière d’un cube découpé. On y voit alors des plumes et des mousses colorées. C’est la mousse au cœur du matelas qui détermine en grande partie si on se réveillera reposé ou tendu. Pour fabriquer ses mousses magiques, Bico travaille avec Foampartner AG. Ce sont eux qui, comme le dit Rocco Cristofaro, s’occupent du « gâteau ». Depuis plusieurs décennies, les machines se trouvent dans un hangar de 120 m de long situé au milieu du village. Elles fabriquent des mousses à base de polyuréthane (PU), que l’on retrouve entre autres dans les matelas Bico, ainsi que toutes sortes de « mousses techniques » comme me l’explique Felix Posavec, responsable développement produit. Il s’agit de mousses pour les sièges de voiture, l’acoustique dans les studios d’enregistrement ou pour la fabrication d’éponges nettoyantes.
Un gâteau de mousse noire est en train de se former. Une monstruosité de plus de 50 m de long, pour être précis. Tout commence par la « pâte », un liquide mélangé à des polyols et des isocyanates. L’ajout d’eau permet de déclencher une réaction chimique. Le liquide qui coule sur une sorte de papier sulfurisé lève en quelques secondes, comme un gâteau à la levure. Après un peu moins de huit mètres de parcours, le liquide noir s’est transformé en un bloc massif de 80 cm de haut. Pour qu’il reste le plus plat possible en haut, une construction métallique vient y presser une autre couche de papier sulfurisé.
Ce gâteau peut atteindre 30 m de long. Il est ensuite coupé à la scie et ses blocs sont déplacés vers la chambre de maturation, une salle sombre avec des dizaines d’emplacements de stockage. L’intérieur d’un bloc de mousse fraîchement fabriqué peut atteindre 180 degrés. Jusqu’à trois jours peuvent être nécessaires pour le refroidir.
Les propriétés finales de la mousse PU sont contrôlées par toutes sortes d’additifs dans le matériau de base liquide. Jusqu’à 20 composants peuvent être ajoutés à Wolfhausen, m’explique Felix. Il dispose ainsi d’un éventail de possibilités bien plus large que les usines de ses concurrents à l’étranger qui utilisent un maximum de cinq à sept additifs. « Cela suffit pour de la mousse standard en grande quantité », explique Felix. Mais les mousses spéciales, comme celles dont Bico a besoin en petites quantités pour ses matelas, sont la spécialité de Foampartner AG.
Dans l’entrepôt, je comprends ce que « petites quantités » signifie pour Félix. Des briques de construction surdimensionnées et des dizaines de blocs de mousse aux couleurs vives y sont entreposés. Un chariot élévateur est en train d’empiler quelques spécimens bleu ciel. « C’est pour notre matelas Clima-Pro », reconnaît Rocco de son œil d’expert. « Particulièrement perméable à l’air, tout en restant stable. » Les couleurs des mousses n’ont pas qu’un but marketing. Plus une mousse est de couleur claire, plus elle est souple. Elles existent dans presque toutes les couleurs de l’arc-en-ciel. Le personnel de l’entrepôt sait exactement à quoi correspondent les couleurs, quelle mousse est destinée aux matelas et quelle mousse est destinée aux applications d’isolation ou d’amélioration de l’acoustique.
Une fois que le bloc de mousse a suffisamment reposé, on le découpe en filets. Ce processus se fait lui aussi à Wolfhausen. Les bords sont redressés afin d’obtenir un parallélépipède parfait dans lequel on vient ensuite découper des couches de hauteur appropriée. Ensuite, des machines de précision fraisent des contours 3D pour les noyaux de matelas à l’aide de couteaux très aiguisés, créant des évidements pour d’autres mousses ou ressorts. Et pour finir, on assemble (en grande partie à la main) les différents composants pour former le noyau fini. Ces produits semi-finis sont ensuite transportés à Schänis chez Bico.
Nous suivons les produits semi-finis pour revenir jusqu’à Schänis. C’est ici que les noyaux de matelas reçoivent leur housse. Son rôle, m’explique Rocco, est capital :
Quand vous vous allongez sur un matelas, vous ne voyez pas la mousse, vous ne pouvez pas la toucher. Votre peau est uniquement en contact avec la housse.
Ici, le travail à la main est de mise. Des couturières expérimentées réalisent la housse à partir de différents tissus sur des machines à coudre. « Chaque tissu se comporte de manière différente, aucune machine ne sait gérer ça. Ça demande un certain feeling », m’explique Markus Läser, responsable de la production chez Bico.
Bico fabrique les matelas à la commande. Chaque noyau est d’abord recouvert d’une sorte de fine chaussette, puis de sa housse. Après deux jours, le matelas est prêt à être livré. Avec un calendrier aussi serré, le mammouth doit pouvoir tenir la cadence. C’est ainsi que s’appelle la machine qui, avec une centaine d’aiguilles fines, fabrique les surfaces de couchage des housses de matelas à partir d’un non-tissé en laine de mouton et d’une bande de tissu qui formera le côté supérieur de la housse. Un ordinateur détermine le modèle à suivre, différent selon le matelas.
On y voit souvent une croix suisse stylisée. Une marque de fabrique, mais aussi un engagement de Bico pour une production en Suisse. « La durabilité commence par la régionalité », affirme avec conviction Markus, directeur de la production, qui prend l’exemple de la laine de mouton. Ce produit, qui auparavant se jetait beaucoup faute d’acheteurs, bénéficie aujourd’hui d’un nouveau marché créé par Bico qui se fournit chez 26 bergeries réparties dans toute la Suisse. Le mammouth traite jusqu’à 850 m de tissu en une journée, soit plus de 450 matelas.
Ce que la machine éjecte atterrit sur de grandes tables avec des machines à coudre. Les couturières utilisent leurs pieds pour contrôler la vitesse à laquelle les aiguilles montent et descendent et leurs bras pour pousser les lourds panneaux de tissu vers l’avant et y poser la fermeture à glissière ou la bordure. Markus reconnaît la valeur de leur travail :
Ce sont de véritables pilotes d’élite.
Leurs missions exigent une grande concentration et une bonne coordination. Ici, ce travail semble réservé aux femmes.
Le travail à la main coûte cher en Suisse. Si Bico continue d’y recourir, c’est parce que Markus et son équipe ont toujours des idées d’amélioration. La couture difficile des coins a été facilitée par une machine à coudre qui coupe le fil juste après la couture. Quand on fabrique des centaines de housses par jour, chaque seconde compte gagnée.
Quiconque fabrique en Suisse ne peut pas se contenter de proposer des produits lambda. C’est Rocco Cristofaro et son équipe de développement qui sont responsables de l’avance de Bico sur la concurrence. À Schänis, il s’occupe de tout ce qui touche à la production. Sur les murs des bureaux avec laboratoire de test attenant, on peut lire les données d’une étude de marché complexe que Bico a fait réaliser il y a deux ans. Il en ressort quatre priorités pour les clients et clientes : ne pas avoir froid ou transpirer, ne pas se réveiller avec des douleurs, le matelas doit durer longtemps et être parfaitement hygiénique.
C’est pourquoi, comme me l’explique Rocco, toutes les housses Bico sont lavables à 60 °C. Pour s’en assurer, les équipes font régulièrement des tests avec une Adora de V-Zug, la machine à laver préférée des Suisses.
En matière de durabilité, la règle veut que l’on change son matelas tous les huit à dix ans. Si le noyau en mousse et les ressorts seraient bien capables de durer plus longtemps, Rocco nous explique qu’après de longues années d’utilisation quotidienne, des résidus peu ragoûtants finissent par s’accumuler (environ 2 kg de déjections d’acariens et autres bestioles). Cela a été déterminé en comparant le poids de matelas neufs à celui de matelas utilisés depuis longtemps.
Avant de lancer un nouveau matelas sur le marché, Bico le soumet à une procédure de test interne. On installe le matelas dans une chambre climatique et on y dépose un « Sweater Body ». Le corps métallique de ce mannequin dégage une chaleur et une humidité similaires au corps humain. La chambre climatique permet de mesurer la rapidité et l’efficacité avec lesquelles l’humidité s’échappe du matelas lorsque le Sweater Body a terminé sa simulation de sommeil.
Dans une autre pièce, un ordinateur évalue et mesure la répartition de la pression d’un corps sur de nouvelles mousses. La couche supérieure arrive-t-elle à bien répartir le poids d’une personne ? Dans quelle mesure la zone des épaules s’enfonce-t-elle ? Le corps est-il encore soutenu au niveau des vertèbres lombaires ? Autant de questions auxquelles Rocco et son équipe cherchent des réponses.
Ce dernier semble trouver l’inspiration pour de nouvelles idées partout. Il se demande ainsi si le système d’amortissement d’une basket suisse très populaire ne pourrait pas être utilisé pour ses matelas. Une nouvelle invention est déjà en production : un sommier dont les lattes ont été tournées de 90 degrés au niveau des épaules, offrant ainsi un meilleur soulagement. « C’était un projet interdisciplinaire comme on en voit dans les livres », explique Rocco, se félicitant de la collaboration avec les employés et employées de la production.
Il décide ensuite de me montrer son « hobby ». Le responsable innovation se transforme alors en Géo Trouvetou. Il me montre un matelas double relié à quelques cartes Raspberry par de minces câbles. Plusieurs petits moteurs électriques réagissent à la pression mesurée qui vient du corps. Comme on bouge en dormant, il faut assurer un soutien et un soulagement aussi précis que possible à plusieurs endroits. Cela pourrait être contrôlé de manière électromécanique. « Mais on n’y est pas encore », m’explique Rocco en riant.
La question du coût environnemental d’un matelas ne peut pas être évitée : à lui seul, le polyol nécessaire à la production de mousse nécessite 60 l de pétrole. Même si d’autres matières premières sont raffinées à partir de cette quantité, cela représente une quantité équivalente de CO₂. Chez Rocco, les noyaux de matelas sont en partie constitués de restes de mousse. Mené par Bico, le secteur commence à proposer des idées sur le recyclage des matelas usés. Mais Rocco l’avoue :
Il nous reste beaucoup de chemin à parcourir.
Des mousses avec des ingrédients de choix, des couturières qui utilisent une machine à coudre comme d’autres piloteraient un avion de chasse. Je commence à comprendre pourquoi les matelas Bico coûtent plus cher que les autres. Cependant, j’ai encore des questions. Rocco est dans le métier depuis suffisamment longtemps pour connaître les astuces qui permettent de vendre un matelas.
« Bien sûr, nous faisons attention à la première impression que donnent nos matelas », m’explique-t-il. Le tissu extérieur de la housse joue ici un rôle important. Lorsqu’une cliente ou un client s’assoit pour la première fois sur un matelas dans le magasin, sa main va toucher ce tissu et la bordure. Les matelas Bico attirent en outre le regard avec leurs motifs piqués de croix suisses. Ce n’est qu’ensuite que l’on s’intéresse à l’intérieur du matelas. Lorsqu’on l’essaie, dans l’idéal avec des vêtements confortables et en prenant son temps, il faut sentir où le corps s’enfonce et où il est soutenu.
Certains fabricants de matelas annoncent sept, voire neuf zones de couchage. Mais finalement, m’explique Rocco, chaque matelas n’a que trois zones : une pour les épaules, une pour la zone lombaire et une pour le bassin. Les fabricants se targuant d’avoir sept zones se contentent d’y ajouter une zone pour la tête. Un bon matelas doit pouvoir créer un équilibre entre l’enfoncement (épaules et bassin) et le soutien (lombaires). Pour cela, il faut placer différentes mousses ou ressorts aux bons endroits. À cela s’ajoutent d’autres couches pour soulager la pression, répartir le poids et assurer l’aération.
Les matelas bon marché ne sont souvent composés que de deux ou trois mousses standard différentes. Selon Rocco, cela ne permet de répondre aux différentes exigences que jusqu’à un certain point. Bien sûr, ces matelas sont moins chers. Les fabricants qui misent sur un petit nombre de produits standard peuvent également économiser des coûts. Si j’avais eu un corps standard adapté, j’aurais probablement pu opter pour un matelas moins cher.
Après une journée passée dans une usine de matelas, je ne vais certainement pas en commander un sur Internet sans avoir pu m’y allonger longuement auparavant. Lorsqu’il m’en faudra un nouveau, je me rendrai en magasin pour discuter avec le vendeur des mousses à froid et du soutien lombaire jusqu’à ce que je sois sûr d’avoir les meilleures mousses pour faire les plus beaux rêves.
Photo d’en-tête : Christian WalkerJe suis journaliste depuis 1997. Stationné en Franconie, au bord du lac de Constance, à Obwald, Nidwald et Zurich. Père de famille depuis 2014. Expert en organisation rédactionnelle et motivation. Les thèmes abordés ? La durabilité, les outils de télétravail, les belles choses pour la maison, les jouets créatifs et les articles de sport.