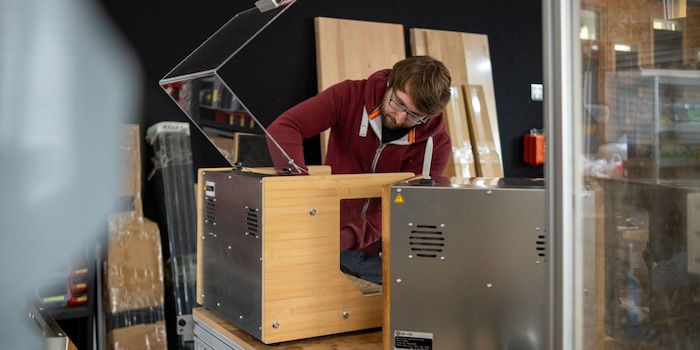
Le rêve de Kevin Buck se réalise : une fraiseuse CNC DIY
Kevin Buck a consacré des milliers d’heures à la réalisation de sa propre fraiseuse CNC de bureau pour inventeurs, adaptée pour le métal. Avec la Kubus Pro, il dispose désormais d’un produit unique en son genre.
C’est dans une rue discrète d’Argovie que se trouve la salle d’exposition de Kevin Buck. Peu visible, car la partie avant sert d’entrepôt à un installateur sanitaire. « Pour l’instant, je n’ai que la partie arrière à ma disposition. Mais bientôt, je pourrai aussi occuper la partie avant », dit-il fièrement.
Kevin a récemment commencé la prévente de sa fraiseuse CNC spécialement conçue pour lui. « Ma fraiseuse comble un vide sur le marché. Elle s’adresse aux inventeurs et inventrices qui cherchent une machine CNC de bureau adaptée pour le métal. » C’est avec ces mots que Kevin m’a incité à visiter son showroom quelques semaines plus tôt.
Arrivé dans son royaume, il me montre le fruit de plusieurs heures de labeur : trois versions préliminaires de la Kubus Pro. « Pour la plus récente, j’attends encore une pièce. » Tout cela fait partie du processus. Kevin n’a cessé d’améliorer la fraiseuse de bureau.
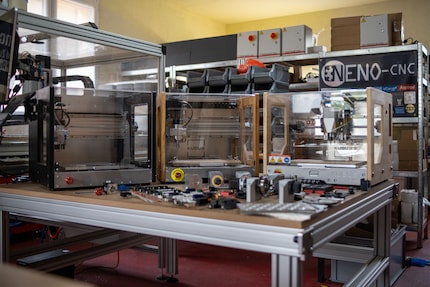
Source : Kevin Hofer
Un hobby devient une activité indépendante
Kevin n’a pas seulement préparé les trois prototypes, mais aussi diverses versions de la commande, de la broche et autres. Il commence tout de suite à me raconter. Chaque pièce de sa machine a une histoire. Par exemple, l’élément de refroidissement du moteur pas à pas. « J’ai essayé plusieurs designs et finalement opté pour un modèle avec des fentes, en rouge. Ça a l’air cool ! »
Mais la coolitude n’est pas tout. Kevin le sait aussi. Il a mis tout son savoir-faire dans la Kubus Pro. « Enfant déjà, j’étais fasciné par les appareils et je les démontais. » Après une formation d’automaticien suivie d’études en électrotechnique, il a travaillé comme planificateur-électricien. Mais c’est en autodidacte qu’il a acquis le plus grand savoir-faire pour la Kubus Pro.
C’est par un ancien hobby que Kevin est arrivé au fraisage CNC. J’ai longtemps été actif dans le modélisme. Avec ma première fraiseuse, je fabriquais des pièces de rechange. Surtout pour mes avions. Comme la communauté de l’aéromodélisme était petite en Suisse, j’ai beaucoup utilisé des quadricoptères. Ils volaient si sauvagement qu’ils étaient régulièrement endommagés et que j’avais souvent l’occasion d’utiliser ma fraiseuse. » C’était il y a huit ans. À l’époque, il avait une fraiseuse filiforme de GoCNC, qui n’était n’adaptée que pour le plastique et le bois. Suite à un déménagement, qui impliquait moins d’espace, il a dû abandonner le fraisage pendant quelques années.
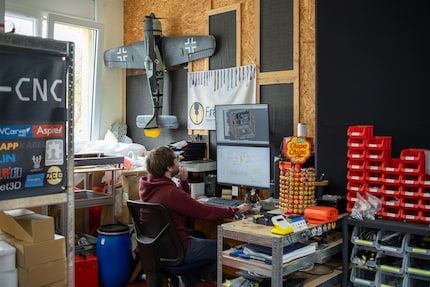
Source : Kevin Hofer
Pendant la pandémie, Kevin a ensuite voulu se remettre au fraisage. En cherchant une machine de bureau abordable, il a constaté que le marché européen n’en proposait pas. « Je me suis demandé : pourquoi ne pas de combler ce manque ? Je me suis alors mis à mon compte à temps partiel. » Au début, il importait des machines de Chine basées sur des systèmes Openbuilds, les adaptait et les développait à sa manière. « Avant, je faisais tout depuis chez moi. Mon bureau et, plus tard, la salle de sport sont devenus des entrepôts. Puis, à un moment donné, je me suis senti à l’étroit et j’ai loué ici. »
De l’adaptation à la création personnelle
Disposant de plus d’espace, Kevin a eu la possibilité de fabriquer ses propres pièces pour ses machines. Il les a ainsi progressivement rendues plus solides et meilleures. « Je voulais rendre les machines plus “suisses”. Donc utiliser plus de pièces issues de la chaîne de valeur suisse. » Il y est parvenu progressivement en renonçant d’abord aux profilés en aluminium venus d’Asie au profit de ceux produits en Europe. Ces fraiseuses sont en effet montées sur ces profilés.
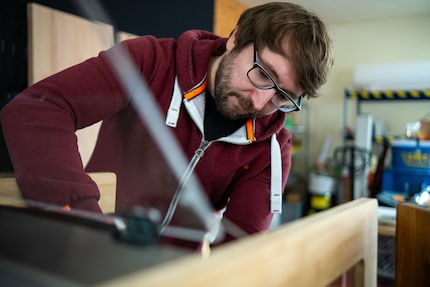
Source : Kevin Hofer
Mais cela lui ne suffisait pas. Il a donc décidé de concevoir ses propres fraiseuses. L’idée de la Kubus était née. C’était il y a deux ans. Au début, il prévoyait de proposer deux modèles : un petit, adapté au bois et au plastique, et un plus grand pour le métal. « Mais j’ai vite constaté que je ne pouvais pas répondre ainsi à mes exigences de qualité. Quelque chose aurait toujours manqué à la petite machine. J’ai donc décidé de fusionner les deux modèles. » La Kubus Pro fait tout ce que le plus grand modèle aurait pu faire, mais elle est un peu plus petite.
C’est ainsi que Kevin a également trouvé sa niche de marché. « En Europe, il n’y a personne qui construit une telle machine à moins de 10 000 francs suisses. C’est la fraiseuse de bureau la plus puissante de sa catégorie. » Cela signifie qu’elle peut être équipée d’une broche de 500 watts avec une vitesse de rotation maximale de 18 000 tours par minute. En plus, elle est très compacte et coûte entre 3000 et 7000 francs suisses. Avec cette broche, il est possible de fraiser du métal sans problème. « Une imprimante 3D permet aujourd’hui de fabriquer des pièces en très peu de temps. Mais celles-ci ne sont pas très stables. C’est là qu’intervient la Kubus Pro ». Elle est destinée aussi aux inventeurs et inventrices qui ont des exigences plus élevées. C’est une machine Swiss Made que Kevin propose, car la chaîne de création de valeur de la Kubus Pro est située à plus de 60 % en Suisse.
Kevin explique que l’aluminium peut être fraisé de deux manières : très lentement ou très rapidement, en enlevant peu ou beaucoup de matière. Il n’y a pas de voie médiane, sinon l’outil serait endommagé. « Avec la Kubus Pro, il est possible d’atteindre facilement des avances de trois mètres par minute dans l’aluminium. Aucun des produits concurrents n’en est capable. Ils font au maximum un mètre par minute avec moins de profondeur d’attaque. »
Les modèles concurrents viennent des États-Unis ou de Chine. Ils sont tous plus instables et plus faibles. Mais la fraiseuse de Chine dispose d’un changeur d’outils. Kevin renonce toutefois délibérément aux gadgets sur la Kubus Pro. « Les machines dotées de nombreux gadgets nécessitent des mises à jour permanentes du micrologiciel, ce que je ne veux pas. Pour la Kubus Pro, il n’y aura jamais de mise à jour de la commande. Elle fonctionne dès le départ, sans gadget. »
L’importance de l’optimisation
Kevin opte pour des matériaux de qualité pour garantir un fonctionnement correct de la machine. Au départ, il voulait monter la Kubus Pro sur des profilés en aluminium. « Ils sont bon marché et simples, mais pas toujours droits. » Comme la précision est importante lors du fraisage, il mise sur des plaques d’aluminium de précision 5083 coulées, fraisées sur les deux faces : « Ça a l’air compliqué, mais elles s’appellent comme ça. » C’est sur ces plaques que sont montés les rails linéaires et les vis à billes.
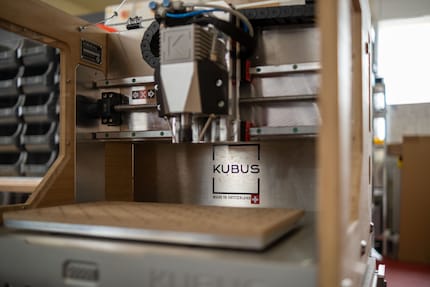
Source : Kevin Hofer
Il s’est également éloigné de son idée initiale pour les panneaux latéraux en bois. Il a commencé avec des panneaux de fibres à densité moyenne (MDF). « Mais ça avait l’air nul. » Il a donc opté pour le chêne. Des menuisiers lui ont ensuite déconseillé cette solution, car le chêne a tendance à se déformer et n’est pas étanche. C’est pourquoi, pour la Kubus Pro, il utilise désormais le bambou multicouche.
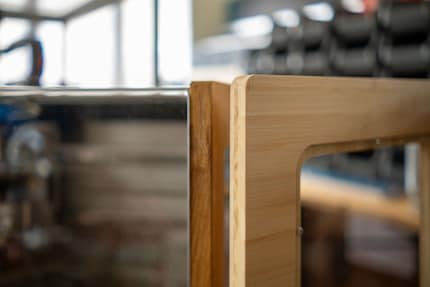
Source : Kevin Hofer
Toutes ces adaptations ont été relativement simples, selon Kevin. Le plus grand défi pour lui a été la conception du circuit imprimé, car il n’avait jamais rien fait de tel auparavant. Il a dessiné le circuit imprimé dans le logiciel KiCad. « Dès la première version, j’étais confiant dans son fonctionnement et j’en ai commandé plusieurs. Mais ensuite, le micrologiciel n’a pas fonctionné parce que j’ai oublié une piste conductrice. » Il n’était pas non plus satisfait des versions suivantes. Non parce qu’elles ne fonctionnaient pas, mais parce que Kevin s’efforçait d’atteindre la perfection. « J’ai optimisé le circuit imprimé de manière à ce qu’il réponde à mes attentes. Il est unique en son genre. Personne d’autre n’utilise un relais de sécurité physique et un arrêt d’urgence côté matériel. »
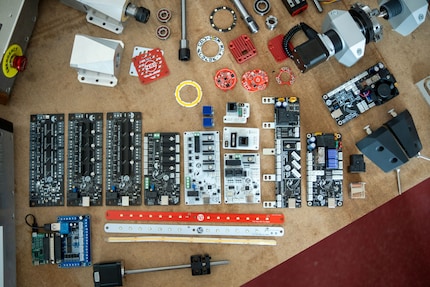
Source : Kevin Hofer
Kevin est tout aussi fier de la commande que de la broche. La conception a nécessité un travail énorme. Je n’avais jamais fait d’ingénierie mécanique auparavant, où les tolérances des roulements et de la concentricité sont importantes. » Il a demandé conseil à des amis ingénieurs, mais il a tout conçu lui-même.
Pour Kevin, il s’agit maintenant de faire en sorte que la Kubus Pro passe les tests de normalisation. « Je suis sûr que ça va marcher du premier coup. J’ai toujours été en contact avec des experts et j’ai tout réalisé selon leurs indications. » Les tests sont prévus dans les semaines à venir. Dès qu’ils seront passés, il pourra commander les pièces nécessaires. Les offres à cet effet ont déjà été demandées.
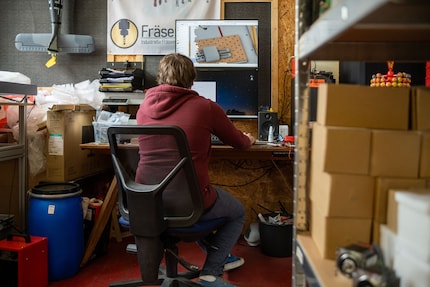
Source : Kevin Hofer
Il lui a fallu deux ans pour être satisfait de tout. Cela correspond à des milliers d’heures de travail. Au début, il devait concilier activité indépendante et emploi salarié. Aujourd’hui, la Kubus Pro est en prévente et Kevin est indépendant à 100 %. « Ce serait super si je pouvais vendre encore plus en prévente. Mais en principe, je ne veux pas devenir trop grand. Seul, je peux en construire au maximum dix par mois. Si j’en vends deux ou trois par mois, je peux en vivre. » Il met également en place une communauté active autour de la machine, grâce à un serveur Discord. Il poste régulièrement des vidéos et des photos de ses machines sur Instagram.
Kevin se focalise actuellement sur ses propres créations. Outre la Kubus Pro, il a réalisé la Nexa Pro et la Triton Next.
Cet article plaît à 373 personne(s)


La technologie et la société me fascinent. Combiner les deux et les regarder sous différents angles est ma passion.